
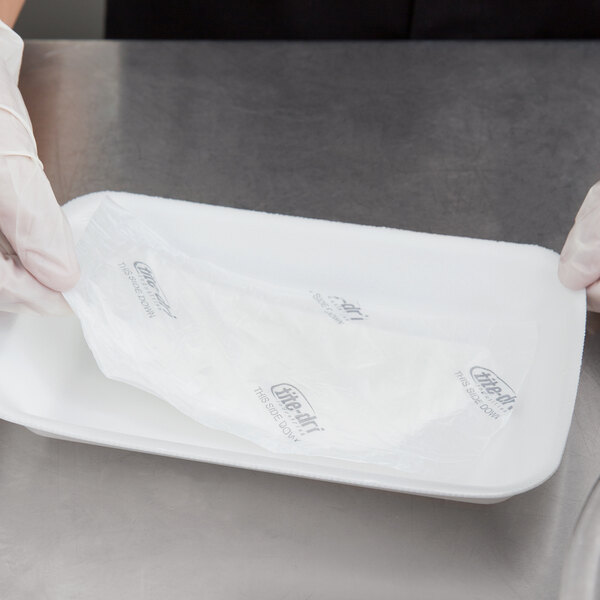
The material is then rinsed to eliminate any remaining contaminants or cleaning agents before it’s ready to be “redeployed” as a manufacturing material.
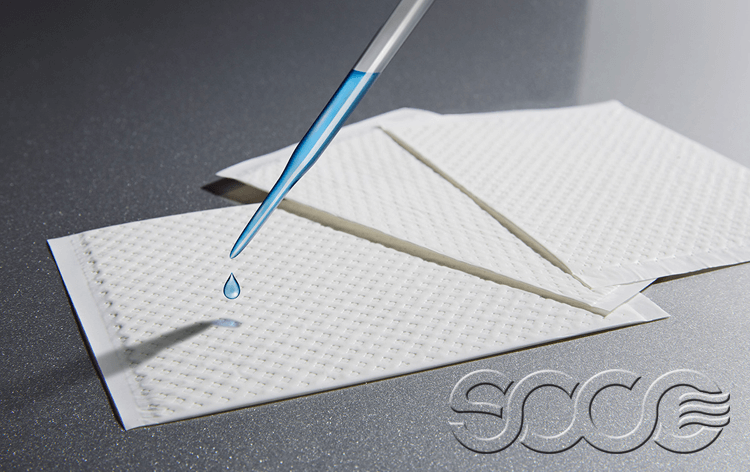
The flakes are then washed, helping to separate any foreign materials, and disinfectants and detergents may be used to ensure complete purity. After PET bottles have been sorted at a recycling centre, the material is ground into “flakes”. Wondering what the science is behind rPET? The process is reasonably simple. The tray sizing is designed to match traditional foam tray sizing to ensure consistency for users and maximise the number of trays facing customers in a meat cabinet or display. The fluid is captured away from the meat to prevent pooling, improve presentation, keep the meat in better condition, and eliminate the need for a plastic-covered soaker pad.įor butchers, this is a quality, sustainable option, while eco-savvy consumers will also appreciate having one less plastic product to dispose of. The hexagonal cells use surface tension to capture and retain fluid to prevent any leakage.

But rPET isn’t the most noteworthy thing about the trays. When it’s recycled, it becomes known as rPET, and can be used to create goods like pallet straps, panelling, carpet and clothing fibres – and now, even meat trays. In Australia, PET is used in a range of products, including water bottles, food containers and shampoo bottles. The secret ingredient in this tray? Recycled polyethylene terephthalate, or rPET.
